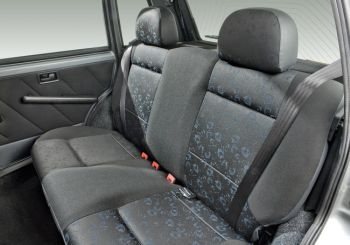 |
Fiat Automóveis is substituting
petroleum-based components in the
manufacturing of all of its car seats; all
vehicles made by Fiat Group in Brazil are
already leaving the site with 5 pct use of
BioFoam, a vegetable based polymer. |
|
|
|
Fiat and
Iveco in Brazil are substituting petroleum-based
components in the manufacturing of all of its car seats.
All vehicles made by Fiat Group in Brazil are already
leaving the site with 5 pct of BioFoam, a vegetable
based polymer that does not compromise durability or
performance of its products.
BioFoam is a
technology that uses renewable resources in the
manufacturing of foam for the automotive industry. The use
of 30 to 40 pct of this resource is under research, but
still has no target date for production.
Polyurethane is
used in the manufacturing of foam for the automotive
industry, but also has many other applications. Usually, it
is based on fossil fuels. Developed by Cargill, the use of
such renewable polyurethane was the result of a partnership
between FIAT Automóveis, Iveco, Lear, TW Espumas and
Isringhausen.
As a key
component of its renewable resource strategy, BioFoam, a
patented technology, substitutes petroleum with plant oils,
in the manufacturing of polyurethane products. This
earth-friendly solution for a full line-up of automotive
interior applications includes; seat cushions, seat fabric
composites, head restraints, arm rests, occupant protection
components, trim cover laminates and overhead systems.
BioFoam is the first mass-production ready, plant-based
polyurethane foam solution, to meet all required customer
performance criteria.
According to Dr.
Hamdy Khalil, Global Director of Research and Development,
and Product Development at The Woodbridge Group, this is
just the start: “BioFoam is the best choice for
environmentally viable automotive interiors. Currently. You
are going to see substantially higher green content levels
in the next generation. We have successfully produced foams
with 100 pct Bio-Polyol in laboratory trials. If the
industry adopted this level, Bio-Polyols alone could reduce
fossil oil dependence by millions of barrels annually. Since
Polyol only represents a portion of polyurethane’s
chemistry, we are now working on the Isocyanate side of the
formulation, to go even more green.”
|