As Fiat and PSA
Peugeot-Citroën present their new light commercial vehicles
at the Sevel Nord plant, the French facility has seen a €440
million investment in the production lines, workshops, a new supply chain and improved
ergonomics.
Main highlights include:
new investment in capital expenditure, mainly for the
body-in-white unit; the workshops modernised and adapted to
the size of the new vehicles; building extensions: 27,000 m2 for the body-in-white
facility, 5,500 m2 for the assembly line; body-in-white assembly 92% automated, representing: 415 robots – 214 of them new and 327 PLCs (programmable logic controllers) – 64 of
them new; Significant improvements to workstation ergonomics:
with a 39% reduction in the number of workstations rated as
heavy and a significant increase in workstations rated
light or medium; Set-up of a new logistics system; 12,000 parts packages delivered daily in 2007, twice the
amount delivered in 2005; Minimised impact on the environment.
An expanded, modernised
body-in-white facility
The body-in-white unit has been expanded by 27,000 m2 to
house the new vehicles dedicated process line and provide
additional logistics capacity, which are essential given the
diverse body styles and different vehicle lengths,
wheelbases and overhangs.
Assembly and quality control processes have been
substantially enhanced with greater automation and improved
ergonomics. The addition of 214 robots and 64 programmable
logic controllers means that the new body-in-white line is
92% automated, compared with 79% for the previous
generation.
Quality control has also been improved by the deployment of
a new 3D measurement station capable of managing the new
vehicles “larger bodies”.
A paint-shop fully altered
for the new vehicles
The new vehicles technical features required changes to be
made to the
paint-shop facilities.
Handling processes have been improved by the installation of
lift tables, overhead and floor conveyors able to support
the weight of the new vehicles.
The curing ovens have been enlarged to accommodate the
larger vehicles.
To house the diverse range of body styles, the two pneumatic
spray guns in the MPV and combi-van paint booth have been
replaced by two electrostatic paint robots.
A flexible assembly line to
manage body-style diversity
The new vehicles have been integrated onto Sevel Nord’s
assembly line which, over the last 10 months, has been
producing the existing LCVs, MPVs and the new generation of
LCVs and combi-vans.
Adapting the line to this wide variety of body styles has
required the implementation of a new supply chain process to
deliver parts to the line just-in-time.
The new vehicles’ heavier weight, varying lengths and
different underbody architecture meant that, to simplify
operator’s tasks, some handling processes required
adjustment by replacing the elevator section for positioning
the body on the chassis and modifying the swing trays.
Windscreen glueing and attachment of fuel tanks and
sub-assemblies have been automated to eliminate heavy
workstations. “Onboard chairs” have been installed at
workstations to allow operators to work seated, with the
necessary parts all within reach.
Improved ergonomics
Several hundred tasks and situations were analysed by Sevel
Nord based ergonomic engineers using the METEO method, which
assesses each situation based on workload (repetitive vs.
cyclical tasks, working environment, …) and then classifies
workstations as “heavy”, “medium” or “light”.
Modernising the production base led to significant
improvements in workstation ergonomics and a 39% reduction
in the number of heavy workstations. In addition, the number
of medium workstations was increased by 17% and light
workstations by 5%.
|
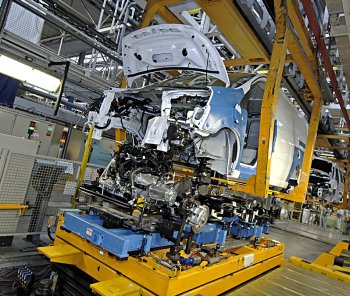 |
The new vehicles have been integrated onto Sevel Nord’s
assembly line which, over the last 10 months, has been
producing the existing LCVs, MPVs and the new generation of
LCVs and combi-vans. |
|
|
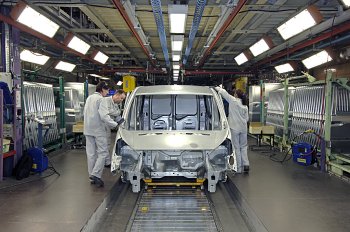 |
As Fiat and PSA Peugeot-Citroën present their new
light commercial vehicles at the Sevel Nord plant,
the French facility has seen a €700 million
investment in the production lines, workshops, a new supply chain and improved
ergonomics. |
|
Operators affected by the decrease in heavy workstations
have been trained to facilitate a quick transition to new
workstations at the Sevel Nord plant.
As part of its social responsibility policy, the Sevel Nord
plant is committed to maintaining jobs for its disabled
employees (21% of the manual employees) and guaranteeing
their long-term employability. Fifteen workstations in the
body-in-white unit have been specifically designed for
employees with disabilities.
A new supply chain process
The supply chain process has been entirely redefined to
enable the delivery of a much greater variety of parts to
the workstations in sequence, within easy reach of the
operators.
As part of this process, the following improvements were
implemented: Standard and special-purpose packaging was redefined, in a
commitment to reducing the quantity of waste cardboard; Packaging size and weight have been reduced to clear space
on the line and improve workstation ergonomics; Small packages distribution has been revised to increase
the delivery capacity at the production line to 12,000
packages per day in 2007, compared to 6,800 in 2005; A 5,500 m2 extension to the assembly unit was built to
meet the floorspace requirements for these organisational
changes.
Municipal authorities from “the Porte du Hainaut” also gave
the go-ahead for a 46 hectares Supplier Park next to the
plant, with a direct 1.2 km track to the assembly line
building.
Five suppliers have already set up facilities in the park: Lear: supply of wire harnesses; Inergy: fuel tanks; Inoplast: new light commercial vehicle’s front and rear
doors; The Ostrovent workshop: manages the sequential delivery of
five families of parts and prepares 12 sub-assemblies; Gefco: the PSA Peugeot Citroën Group’s transport and
logistic division has a 20,000 m2 facility to support the
419 trucks that supply the Sevel Nord plant every day.
Enhanced environmental
protection
The Sevel Nord plant was ISO 14001 certified in 2000. All of
the environmental factors related to the manufacture of the
new range of compact light commercial vehicles and combi-vans
were integrated in the project from the beginning. The main
improvements in Sevel Nord’s environmental performance are:
A reduction in paint solvent
waste: Paint solvent waste has steadily declined, from 13.75 kg per
vehicle in 1996 to 6.09 kg in 2005, with further reductions
being driven by the recent modernisation of the paint-shop.
A reduction in water
consumption:
Water consumption has decreased from 8.31 m3 per vehicle in
1994 to 2.3 m3 in 2005. The increase of new vehicle
dimensions was integrated into the search of technical
solutions to reduce water consumption (i.e. more precise
spraying as each vehicle goes down the line and the
introduction of water recycling).
Quieter facilities:
The choice of new installations has been carefully
considered to limit and monitor noise impact levels on the
plant and its surrounding environment .
A reduction in waste and an
increase in sorting and resource recovery:
Reducing packaging waste is a key concern at Sevel Nord and
the new project integrates the use of sustainable packaging
materials for parts deliveries. The objective is to reduce
packaging waste to 6 kg of cardboard per vehicle, compared
with 7.5 kg in 2005.
In addition, the total percentage of recovered waste is
expected to remain high thanks to an increase in waste
sorting and optimised use of resource recovery services.
|
|
|