With
the Sportiva Latina chassis, these problems were faced using
multiple layers of non-woven carbon mats, with 0°-90°
fibre orientation, and adding a special binder compatible
with epoxy resin to maintain the dry lay-up in the die
before the resin transfer. Additionally, the ply sequence
was optimised not only versus structural performance but
also to improve wet fibre ability.
For the same reasons, the RTM process was vacuum and heat assisted: die and resin temperature as well injection and vacuum points were accurately tuned. The resulting component seemed to match the structural requirements well in terms of homogeneous distribution of reinforcement and fibre to resin ratio: static and durability tests are still running to assess the full performance.
Regarding the assembly of composite parts to the metal front and rear ends, the low production rate allowed manual joining operations to be considered, mainly based on screwing (titanium bolts) and adhesive bonding (two-component adhesive with curing at room temperature).
The composite floor of the prototype and the firewall both featured metal bushes integrated in the parts during the forming process, in order to allow application of the bolts. Due to the high loads and the complex geometry, the composite floor and the firewall joint was designed in an overlap configuration with application of both bolts and bonding joining technologies.
As for manufacturing the metal front and rear ends, technological aspects versus series production requirements were not fully exploited
on the project: green sand instead of vacuum processes were used both for Al and Ti castings, Ti and Al profiles were adopted instead of actual extruded profiles.
Nevertheless, the first chassis prototype allowed engineers to assess the goal of weight saving: the whole structure, neglecting the unsprung masses, weighed only 98 kg, meeting the initial target perfectly.
|
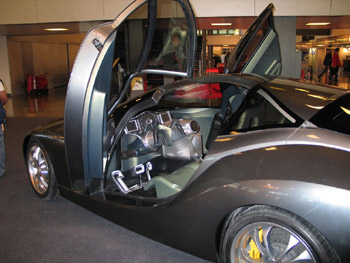
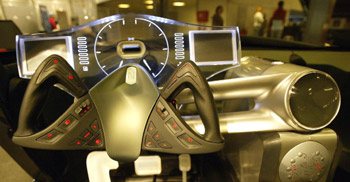
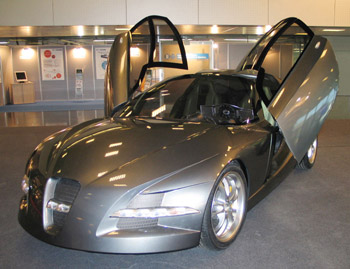 |
The
'A'-post of the Sportiva Latina is reminiscent of
the Alfa Romeo SZ. Access to the interior is
gained by upward swinging doors. |
 |
|
|
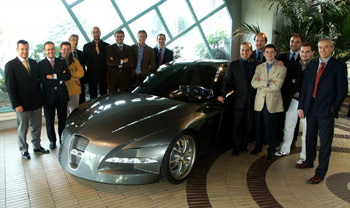
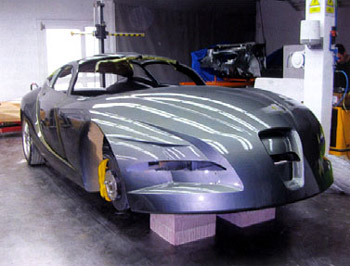 |
Top:
The team of engineers at CRF present their
finished project. Construction of the prototype
was carried out by Mazel engineering, with the
finishing touches being added the evening before
the unveiling in Barcelona. |
 |
|
Unfortunately, the prototype’s expense (only two multi-material split-frame chassis have been built) and undefined technologies rules out any tests for crashworthiness, but FEM analysis has shown a correct behaviour in full and overlap frontal crashes, as well as rear impact.
Sportiva Latina by-wire systems: the integrated development of mechatronic solutions to high performance motoring
The layout of the bodywork and the principal systems of the Sportiva Latina were obviously influenced by the car’s ambitious technology.
It was highly important that the car delivered perfect stability under all conditions, even with its compact suspension system as a result of the split-frame layout. Another problem focused on relaying the power generated from the
440 bhp Maserati V8 VVA engine with robotized transmission to each of the four wheels via an active differential.
The concept of Latin sportivity is likened by the engineers as uniting the devil with holy water: a balance must be found between maximum performance with comfort, safety, ease of handling and a communicative chassis.
In order to find a new driving sensation, as well as a new emotion and relationship between the driver and vehicle, the engineers at CRF carried out detailed analysis on all the chassis systems and innovative technologies developed up to the present day.
The process was led from a performance-based perspective in order to develop advanced solutions and to radically integrate the car’s systems.
It was effectively deemed necessary to carry out specific activities on the development of:
a) suspension layout; b) steer-by-wire; c) active rear differential
and d) Ego-Mode strategy.
Mazel
Engineering
After the styling had been decided, the Sportiva Latina was computer modelled and the CAD data was sent to Mazel Engineering in Barcelona for the construction of the prototype. In typical fashion, the car was finished the night before the show, where it was unveiled to the press complete with opening doors, finished interior and operational Occiocentro system.
by Paddy Granger
|
|
|