THE MAJOR
CONTRIBUTION OF THE FIAT GROUP'S COMPANIES
|
To achieve its
goal, the company deployed its best resources and ensured
that maximum quality and reliability standards were applied
throughout the product development and construction process.
It also developed a profitable co-operative relationship
with its outside suppliers and some Group Companies
including Fiat Powertrain Technologies, Teksid, Magneti
Marelli, Elasis, Comau and Centro Ricerche Fiat. The work
done produced the many innovative solutions that make the
Grande Punto the new benchmark for its category.
Fiat Powertrain Technologies
Fiat Powertrain Technologies developed the complete engine
control system for the 1.2 8v and 1.4 8v Fire petrol engines
for the Grande Punto (ECU, intake manifold with throttle
valves, injectors, petrol pipes and sensors). The electronic
control unit, mounted on the engine, is of a new generation.
For the diesel engines, it supplied the "heart" of the
system governing the new 75 bhp and 90 bhp 1.3 Multijet
engines (software and hardware for the electronic control
unit). The company's contribution where engine control is
concerned also included the development of the power
assisted gearbox for the petrol and diesel versions.
Founded early in 2005, Fiat Powertrain Technologies is a new
industrial company located in Turin that draws together the
Group's capacity for innovation and its experience in the
field of engines and gearboxes. A new business that is open
to the outside world. Present in 12 countries with 26 plants
and 16 research and development centres, the company has
absorbed the resources, employees and activities of Fiat
Auto Powertrain, Iveco Powertrain, Magneti Marelli
Powertrain, Iveco Motoren Forschung and the Powertrain
activities of Centro Ricerche Fiat and Elasis.
Fiat Powertrain Technologies began operations with sales of
over Euro 6 billion, over 20% of which to external
customers, and is expected to develop considerably in the
future. It can count on over 23,000 employees, 11,000 of
whom from Fiat Auto, 7,200 from Iveco, 3,800 from Magneti
Marelli Powertrain, and over 1,000 from Centro Ricerche
Fiat, Iveco Motoren Forschung and Elasis.
With an annual output of over 2,200,000 engines and about
2,000,000 gearboxes, and a very broad range in terms of
power outputs and applications, Fiat Powertrain Technologies
plays an important role in the automotive world. And we
cannot ignore the fact that being able to rely on such a
large number of state-of-the-art research and engineering
centres will bring considerable advantages to the
development of innovative products that are highly
competitive in terms of performance and cost. The activities
are managed in the following strategic areas:
- development of markets outside the Fiat Group;
- enhancement of the centres of technological excellence and
systematic transfer of the results to the product range;
- integration of engineering capabilities from the product
development stage to experimentation, and management of
operating products;
- synergies in the industrialisation and manufacturing
processes;
- synergies in purchasing, thanks to innovation,
technological rationalisation and higher volumes;
- focus investment on the research and development of
environment-friendly engines: methane, hybrid, fuel-cell.
Teksid
The crankcase and crankshaft for the 1.2 8-valve and 1.4
8-valve Fire engines, and the crankcases for the 1.3 and 1.9
Multijet engines, are produced in the Crescentino (Vercelli)
foundry.
Magneti Marelli
Magneti Marelli has made an important technological
contribution to the development of the Grande Punto,
developing innovative systems and components as it has for
other recent Fiat Auto models. All the business lines were
involved in the project, starting from the exterior, for
which Automotive Lighting designed the red rear lights
(brake lights, side lights and direction indicators) which
are positioned at the top of the car at the sides, linking
the roof, the sides and the tailgate, and providing a strong
stylistic imprint. The foglights were designed using the
latest technologies and they blend perfectly with the
styling of the Grande Punto, becoming a distinctive
stylistic feature of the front.
Comfort in the passenger compartment is enhanced by the two
control panels that Magneti Marelli developed for different
outfits. The basic panel features a segment/alphanumerical
monochrome LCD display which shows the main data regarding
the trip, the set-up and the operation of the car. It also
includes a speedometer and electronic rev counter, fuel
level gauge, engine coolant temperature, and a B-Can
connection to exchange data with the rest of the vehicle and
the diagnostic system. The 'high line' version has a
monochrome dot matrix display, which shows the pictograms of
the navigation system when this is present. The Grande Punto
also adopts a hands-free telephone kit which can interface
with mobile phones and other devices with Bluetooth
technology, by connecting the mobile phone to the car's
wireless system and exploiting the onboard audio system.
Fiat entrusted the development of the suspension system to
Magneti Marelli; it is based on the classic layout of
MacPherson struts at the front and a torsion axle at the
rear. The technological commitment was distributed in
various parts of the world, involving research and
manufacturing centres in Italy, Brazil and Poland. A
crossbeam and a wishbone that guarantee performance worthy
of segment C at extremely competitive costs were developed
in Turin. Machining operations will take place in the
Italian plants of Rivalta and Sulmona, and panelling in
Melfi, where the suspension is assembled using new
manufacturing concepts that adapt to customers' daily
requirements.
Magneti Marelli has developed the complete exhaust system
for all the Grande Punto engines ('hot end' system linked to
the engine, and 'cold end' system linked to the floorpan).
The most significant novelty regards the system created for
the 1.2 and 1.4 8-valve engines, which comprises a
semi-shell steel manifold and a compact catalytic converter;
it respects Euro 4 standards and adopts particular engine
control and calibration strategies to reduce consumption.
Elasis
Elasis' contribution to the development of the Grande Punto
regarded three main areas:
fine-tuning
and use of the 'Hardware In the Loop Virtual Car' simulator
to test the software of the braking system control units
(ABS and ESP versions) and the petrol engine controls (1.2
and 1.4 FIRE);
support to
manufacturing start-up in the Melfi plant;
co-design
with suppliers, approval and certification of all the petrol
engine control units and the control units of the robotised
gearboxes (not available at the launch).
Where the first
area is concerned, we should underline that the Grande Punto
is Fiat Auto's first car to benefit from a new test
methodology based on an HIL simulator and known as 'Virtual
Car'. It is a highly complex system which has taken three
years to develop, and is the state of the art for tests to
verify the integration of the electronic control unit,
checking that the various electronic systems on the vehicle
interact correctly.
This verification is not only performed in nominal test
conditions, but also in extreme conditions that cannot be
created on the car (for example, breakage of a sensor while
the car is taking a corner at 100 km/h). The test
sequence can be carried out automatically, so it is possible
to perform several test cycles gradually modifying certain
parameters (such as the vehicle speed), and verifying the
robustness of the software in greater detail. Automation
makes it possible to reduce verification times or to perform
more test cycles in the same amount of time. All of which
has obvious advantages for product quality. In just a few
months, 40 software bugs were filtered out, which it would
have been difficult to intercept with standard test
instruments.
The second area involved technicians and experts in
electrical and electronic problems; they worked alongside
their colleagues at Fiat Auto to diagnose the anomalies
found on the cars that underwent the TOC test (from the
customer's viewpoint) and the RG (Reliability Growth) tests.
In the third area, Elasis worked in co-design with
suppliers, developing, approving and certifying the software
of several control units: petrol engine controls of the Fire
1.4 (with variable valve timing) and Fire 1.2 engines, and
of the Selespeed M20 and C514 robotised gearboxes (not
available at the launch).
The innovative features, which are the result of both the
vehicle's unusual architectures (the first and only time it
has been used by the Fiat Group) and the presence of
continuous variable valve timing (the only case in Europe on
an 8v engine), entailed the constant commitment of highly
qualified personnel. This made it possible to reach
ambitious objectives in terms of functionality, sturdiness,
performance and consumption. And finally, part of the
approval tests were performed using Hardware in the Loop
simulators for individual sub-systems; the main advantages
of using these tools are the same as those of the Virtual
Car.
Comau
Comau has always been Fiat Auto's partner for the
development of car production systems, and it was involved
in all stages of the Grande Punto project.
|
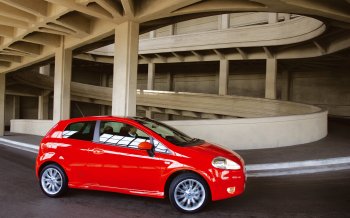
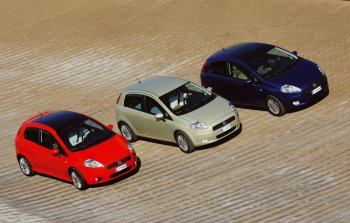
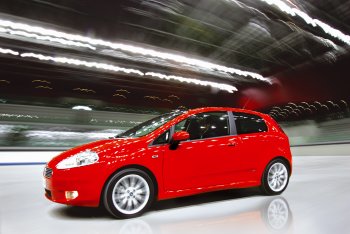 |
|
|
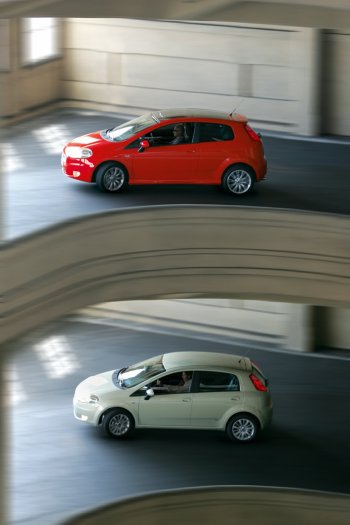 |
|
To start with, the Product and Process Engineering Business
Unit collaborated with the Engineering department to define
the vehicle's layout and architecture, to develop the
chassis and bodywork and all the mechanical systems for the
chassis (car suspension, engine suspension, drive shafts,
brakes, exhaust, fuel system, controls, steering, pedals,
cooling and air conditioning). Subsequently, it adopted its
own calculation methods to carry out virtual validation of
the facia and the related assembly methodologies. After
sophisticated technical analysis, virtual simulation and
calculation to optimise the product, Comau built the dies
used to manufacture the facia.
Comau's Sheet Metal Dies and Plastic Moulds Business Units
developed the manufacturing dies for the front bumper and
central pillar, and the prototype tools to fit the front
bumper and bonnet. The Welding Systems Business Unit built
the assembly lines for the entire bodyshell and related
subassemblies. We should underline the use of three remote
laser welding systems (Agilasertm) to weld the internal
skeleton of the mobile parts.
A total of 310 new generation SMARTm robots were used on the
assembly lines. Robotised solutions were developed using
different models of Comau's robot range: the SMART NH4, the
top of the Comau Robotics spot welding range, featuring
"hollow wrist" technology (containing all the wires,
extremely efficient performance, outstanding flexibility and
100% off-line programming), the SMART NH1 for manipulation
and aesthetic spread applications, and the SMART NS for arc
welding. And finally, it prepared assembly lines for the
automatic coupling of the mechanical organs with the painted
bodyshell.
Centro Ricerche Fiat
The Multijet engine
The new 1.3 Multijet diesel engine and the relative control
system were created by CRF in the late 90s, together with
the engine control strategies which make this engine unique
in performance, consumption and emissions. The Multijet
system is protected by over 30 international patents.
The excellent performance and the simultaneous, substantial
reduction in emissions of CO2 and other harmful gases are
the result of a combination of factors: - the adoption of a
second generation Common Rail technology (Multijet); - the
design of a cylinder head with 4 valves per cylinder and
high swirl values; - the optimisation of the combustion
chamber. During the design stage, advanced calculation
techniques and three-dimensional simulation were used
extensively for the fluid dynamics, injection and combustion
processes, which are the cornerstones of the engine's
operating system.
Painstaking design of the structural part of the engine and
carefully targeted experimentation, combined with the
potential of the Multijet technology made it possible to
guarantee not only complete reliability of the engine over a
long period, but also excellent acoustic comfort which is
indispensable to achieve a high level of comfort in the car.
An innovative telematic system
The Grande Punto will be one of the first cars from Fiat
Auto to offer an innovative telematic system developed by
Fiat and Centro Ricerche Fiat. The basic version of the
system (which will be available at the launch of the car),
incorporates the functions of a Bluetooth hands-free device
with an evolved, comprehensive voice interface.
The high quality of the voice interface has been achieved
using innovative methodologies developed by CRF to
experiment and verify Voice Control Systems. These
methodologies make it possible to optimise the performance
and usability of synthesis and voice recognition systems
necessary to interact with the car's info-telematic systems.
CRF methodologies
To build a revolutionary engine, innovative systems and,
more generally, successful cars, a company needs innovative
methodologies that make it possible to interpret the
customer's wish for distinctive comfort and performance that
differ from those of the competition, low consumption and
emissions in all conditions, and the highest levels of
safety, quality and reliability. To do this, CRF has
developed new methodologies and has transferred them to the
Fiat Teams who designed and developed the Grande Punto.
CAE methodologies for multi-objective analysis of the
chassis
CRF provided CAE support for the development of the entire
chassis, particularly to meet the performance targets in the
fields of fatigue resistance and NVH quality. The chassis'
resistance to fatigue was developed and calculated,
virtually simulating the typical missions that cause fatigue
using FEM models that are already employed for experimental
bench testing; subsequent experimental verification
confirmed the results of the calculations.
The close consistency between the calculations and the
experimental results, was achieved by combining multi-body
calculation methodologies (dynamic simulation of the car in
its mission) and FEM calculation methodologies (structural
calculation of stress and fatigue damage).
Where NVH is concerned, CRF's contribution regarded the
elements perceived by the customer in particular. This
covers the virtual test activities related to steering wheel
vibration (crossbeam and steering column), engine noise
(structural changes to the anchorage area) and advancement
noise (suspension blocks and bushes). The approach was based
on the use of FEM calculation models, and the related
optimisation processes, and was supported during validation
by dedicated experimental protocols, making it possible to
control the development of the most critical subassemblies
and to follow their evolution right down to the final tests
on prototypes. The reliability of the numerical
methodologies used made it possible to identify improvements
and to then engineer them, within a panorama of extremely
stringent constraints (weight, technological feasibility and
more), related to the many performance values demanded of
the component under examination.
-
The Quality
Indices (IQ), which make it possible to link the
vehicle's technical characteristics with the customer's
perception, and therefore to design a car with the user
in mind, consistent with the company's brand values.
-
Target
setting-deployment-achieving targets, which start from
the set customer objectives and translates them into
technical design objectives for the various systems on
the vehicle: engine, suspension, bodyshell, interior,
etc..
-
Multidiscipline structural optimisation, which makes it
possible to optimise the project with efficient
structures, maximising performance and minimising
weight.
-
Crash and
biomechanical methodologies ensure that the passenger
cells effectively protect the occupants and that the
front of the car is compatible with vulnerable subjects
(pedestrians, cyclists, etc.), respecting the demands of
current and future legislation.
-
Computational fluid dynamics make it possible to
optimise the exterior aerodynamics of the vehicle to
benefit fuel consumption and aerodynamic noise, but also
to define interior comfort and well-being in terms of
climate and air quality.
-
NVH methods
(Noise-Vibration-Harshness) that minimise noise and
vibration, making the passenger compartment comfortable
and quiet in all conditions, reducing stress, to the
benefit of the driver's health and attention.
-
Vehicle
handling methodologies, a hallmark of Fiat, Lancia and
Alfa cars, have made it possible to achieve an
enjoyable, predictable drive in all speed, manoeuvring
and grip conditions, through painstaking design of the
suspension and controls (steering, brakes, etc.).
-
Physical and
cognitive ergonomics, supported by the Virtual Reality
laboratory, are employed in the correct design of the
interior space and systems (seat, facia, etc.), the
primary and secondary controls, the mobile parts and the
communication interfaces, which establish the
interaction between the driver and the vehicle from the
design stage.
In addition
to the methodologies: an innovative manufacturing process
In Melfi, three Comau AGILASER systems weld the skeleton of
the front and rear doors of the Grande Punto. In the late
1990s, research into new applications for laser
technologies, conducted by CRF specialists, led to a joint
project between Fiat Auto and Iveco, to evaluate the
technical and economic aspects of the potential applications
of remote laser welding. CRF and Comau then promoted a
project to develop the technology, involving other leading
companies in the laser systems field. The skills and
activities developed by Comau specialists were decisive to
achieve the flexibility, productivity and reliability in the
manufacturing field that basically represent the competitive
advantage of the AGILASER system.
The evolution of laser technology made it possible to
develop high productivity and high efficiency welding
systems that use the properties of the laser to weld
bodywork sub-assemblies. These systems do not need optic
fibres or robots to transport the laser beam, which is
directed at the spot being treated by means of mirrors.
Because there is no significant inertia, it is possible to
reduce the time necessary to move the laser beam from one
weld spot to another to a bare minimum.
This means a significant reduction in the time for each
cycle and in the areas occupied compared to resistance spot
welding; a further benefit is obtained in terms of the
product; because there is no welding calliper, the shape of
the join can be optimised on the basis of the stress (in
addition to circular welds, it is possible to make linear
welds of different lengths), which improves resistance and
lightens components. As a whole, the innovations that CRF
has transferred to Fiat Auto, and which are contained in the
new model, are protected by over 50 patents (including the
Multijet patents). |
|