A VERY COMPREHENSIVE
ARRAY OF SOPHISTICATED ENGINES AND GEARBOXES
|
Behind the
strong personality of its styling, the Grande Punto offers a
comprehensive range of excellent engines featuring advanced
technology and generous performance. There are two petrol
engines (1.2 8v delivering 65 bhp and the 1.4 8v delivering
77 bhp) and four Multijet turbodiesel units: the 75 bhp or
90 bhp 1.3 16v, and the 120 bhp or 130 bhp 1.9 8v. Each has
different features which are exploited in full in
combination with 5 or 6 speed mechanical gearboxes, which
stand out for their generosity, sparkling character, high
performance and sophisticated technology. The features they
share are outstanding reliability and respect for the
environment: all the engines respect Euro 4 emissions
limits.
All the Grande Punto engines are built by Fiat Powertrain
Technologies, the Group's new operating sector. FPT groups
together all Fiat Auto's activities in the fields of
innovation, research, planning and production of engines and
gearboxes for all types of application, from cars to
commercial vehicles, boats and agricultural machinery. More
than 3000 work in the FPT research centres in eight
different countries and they help to make this sector a
great centre of technological excellence and constant
innovation.
Diesel engines: the history of Fiat's achievements
The 75 bhp and 90 bhp 1.3 16v Multijet
The Fiat Punto could not fail to mount the 1.3 16v Multijet
- the smallest and most advanced second generation direct
injection Common rail diesel engine - now with an important
novelty: a new version with a variable geometry turbo is
making its debut. With this turboboost system, the 1.3 16v
Multijet delivers a power output of 90 bhp (66 kW at 4000
rpm) and peak torque of 20.4 kgm (200 Nm at 1750 rpm). That
is not all. With the 90 bhp 1.3 Multijet, the Grande Punto
achieves outstanding performance: it has a top speed of 175
km/h and accelerates from 0 to 100 km/h in just 11.9
seconds. Even consumption is among the lowest in this
segment: 5.9 l/100 km in the urban cycle, 3.9 l/100 km out
of town and 4.6 l/100 km in the mixed cycle.
The new engine differs not only for the different turboboost
system (on the 75 bhp 1.3 Multijet it is provided by a fixed
geometry turboblower), but also for other changes. The
combustion system has been modified, increasing the
permeability of the inlet and exhaust manifolds, reducing
turbulence in the combustion chamber and varying the
geometry and the compression ratio from 18:1 to 17.6:1. The
emissions control system envisages an EGR valve with
electric actuation managed directly by the engine control
system, a heat exchanger to cool the recirculating exhaust
gas (EGR), and a 'close coupled' catalytic converter, which
guarantees respect for EC Phase 4 emissions limits.
The performance of the 1.3 Multijet is also excellent; it
delivers a power output of 75 bhp (55 kW at 4000 rpm) and
peak torque of 19.4 kgm (190 Nm at 1750 rpm). With this
engine the Grande Punto has a top speed of 165 km/h and
accelerates from 0 to 100 km/h in 13.6 seconds, with
excellent combustion: 5.9 l/100 km in the urban cycle, 4.0
l/100 km out of town and 4.7 l/100 km in the mixed cycle.
These are the differences between the 75 bhp and the 90 bhp
versions. On the other hand they both share the engine
architecture: 4 cylinders in line, 1248 cc, with a bore of
69.6 mm and a 'long' stroke of 82 mm. There are four valves
per cylinder, driven directly by twin overhead camshafts via
rocker fingers with a roller. That is not all. The 1.3
Multijet 16v is a masterpiece of technology in miniature:
complete with all its accessories, it weighs just 130 kg,
and is also small in size, just 50 centimetres long and 65
centimetres high, with the components laid out to take up as
little space as possible.
Designed to criteria of maximum rationality, efficiency and
reliability, the engine is capable of excellent performance,
and is practically built 'for life': it was designed to
travel 250,000 km without any maintenance to the mechanical
components. What is more, the oil change intervals have been
extended from 20,000 to 30,000 km (the 1.3 Multijet 16v uses
low viscosity oil, which means more fuel economy, and it
respects the environment). This compact, technologically
sophisticated engine is also environment-friendly, because
it meets Euro 4 emissions limits even without a particulate
trap, which is available on request for certain markets.
The 1.3 Multijet 16v (whether 75 or 90 bhp) therefore
represents a real leap forward in technological terms, and
this translates into lower fuel consumption and emissions
for the customer. Without even considering the increased
quietness (due to the multiple injections), the enhanced
comfort (fewer alternating masses mean less vibration), the
smoothness and enjoyment of driving it (due to the extremely
smooth torque delivery, that comes from better control over
combustion), elasticity and the prompt response of a diesel
unit which resembles a petrol engine because of the vast rev
range (for example, the driver is no longer aware of the
'fuel cut-out' just above 4000 rpm), the
environment-friendly features that enhance the diesel's
great quality on the environmental front (consumption) and
keep its main defect (particulate emissions) to a minimum.
The 120 bhp and 130 bhp 1.9 Multijet
Both engines have 4 cylinders in line, and two valves per
cylinder, with a bore of 82 mm and stroke of 90.4 mm. The
first delivers 120 bhp (88 kW) at 4000 rpm and torque of
28.5 kgm (280 Nm) at 2000 rpm; the second delivers 130 bhp
(96 kW) at 4000 rpm and torque of 28.5 kgm (280 Nm) at 2000
rpm. Several changes were made to the two engines to
increase performance and engine torque at low speeds, and to
reduce noise and vibration. For example, the "Common Rail"
system envisages two automatic control strategies for the
setting and balance of the injected diesel fuel, which
reduces noise and vibration. The turboboost is provided by a
variable geometry Garrett VGT 17 turboblower with electronic
control that helps to improve the power delivery, but also
generates very high torque at low engine speeds. In fact,
90% of peak torque is available between 1750 and 3250 rpm.
These figures translate into extremely enjoyable driving and
brilliant performance: powered by the 120 bhp 1.9 Multijet
engine, the Grande Punto Emotion has a top speed of 190 km/h
and accelerates from 0 to 100 km/h in 10 seconds (the values
for the Sport version with the 130 bhp 1.9 Multijet engine
are 200 km/h and 9.5 seconds). Brilliant performance, but in
spite of this, fuel consumption remains low: 7.5 l/100 km in
the urban cycle, 4.5 out of town, and 5.6 in town (the
values for the 130 bhp 1.9 Multijet are 7.6, 4.6 and 5.7).
Last but not least, both the 1.3 Multijet and the 1.9
Multijet mounted on the Grande Punto respect Euro 4
legislation and offer a particulate trap (DPF), a 'for life'
system that eliminates fine dust and does not need additives
to regenerate it.
The Multijet system on the second generation JTD engines
The Multijet turbodiesel engines mounted on the Grande Punto
are jewels of modern engineering which confirm Fiat Auto's
leadership in this field. When it developed the Multijet
system, the Fiat Group set an important new record in the
field of diesel engines, made possible by the huge amount of
expertise accumulated since 1986, when the Croma TDI was
launched, the world's first direct injection diesel-engined
car. For those years it was a brilliant result, the first
important step forward towards more efficient combustion in
the field of diesel engines for cars. Thanks to this
technology, which other manufacturers soon adopted, diesel-engined
cars were able to guarantee both better performance and
lower consumption. One problem remained: the excessive noise
made by the engine at low speeds and in 'speed transients'.
This is where the history of the Unijet starts, or rather
the search for a more evolved direct injection system, which
could drastically reduce the problem of noisy combustion.
After a few years, this research produced the Unijet, but it
also brought other advantages in terms of performance and
consumption. There were only two possible ways of solving
the problem: passive acceptance, isolating the engine to
prevent the sound waves from spreading, or working actively
to eliminate the problem at source, developing an injection
system that could reduce combustion noise. Having chosen the
second strategy, the Fiat engineers immediately concentrated
their research on the 'Common Rail' principle, excluding
other high pressure injection systems after careful
analysis. The other systems did not allow the pressure to be
managed independently of the rpm and the engine load, nor
did they envisage pre-injection, the two strengths of the
Unijet. The theory that the engineers started to analyse was
both simple and ingenious, the fruit of work done by
researchers at Zurich University, which had never been
applied on a car. By continuing to push diesel fuel into a
tank, pressure builds up inside the tank, which thus becomes
a hydraulic accumulator, or 'rail', in other words a reserve
of pressurised fuel, ready to use.
Pre-industrialisation of the Unijet, the system developed by
Magneti Marelli, Centro Ricerche Fiat and Elasis on the
basis of the Common Rail principle, began three years later,
in 1990. This stage was concluded in 1994, when Fiat Auto
decided to choose a partner with great experience in the
field of injection systems for diesel engines. The project
was therefore sold to Robert Bosch for the final part of the
work, i.e. completion of the development process and
industrialisation. In October 1997, eleven years after the
Croma TDI, another record-setting car went on the market:
the Alfa 156 JTD equipped with a revolutionary turbodiesel
engine that gave hitherto unimaginable results. The cars
equipped with this engine were incredible quiet, with a
sparkling response on a par with that of a petrol engine and
performance levels that were 12% higher than those of a
similar pre-combustion engine, as well as 15% lower
consumption. The success of the Alfa 156 with the JTD engine
was immediate, and very soon not only was it being used on
other Fiat Auto models, but numerous other car-makers were
adopting similar engines. Now it is the turn of the second
generation of JTD engines, the Multijet multivalve units.
The underlying principles of second generation turbodiesel
engines remain those of the Common Rail, i.e. high injection
pressure and electronic injector control. But one extra
feature has been added: during each engine cycle, the number
of injections increases over and above the current number of
two. In this way, the same amount of diesel is burnt inside
the cylinder but in several portions to achieve smoother
combustion. The advantages include lower running noise,
reduced emissions and a 6-7% increase in performance. All
this comes with a level of engine efficiency that improves
car handling still further. These results are not to be
underestimated, particularly because they are obtained with
an engine that represents an incredible leap forward from
pre-chamber diesels and even improves on first generation
JTD engines.
The secret of the Multijet engine lies in the control unit
that governs the electric injector opening and closure
system (and also in the injectors themselves). The crucial
element is the electronic control unit itself that can
perform a set of injections that may be very closely spaced.
Fiat Auto's researchers developed the part (together with
the injectors) especially for this application. It is
designed to deliver the multiple injections that assure more
accurate control of pressures and temperatures developed
inside the combustion chamber and also more efficient use of
air taken into the cylinders. This enables further goals to
be achieved: quieter combustion, reduced emissions and
increased performance.
The Multijet system is underpinned by long years of
research. Our engineers began by resolving the problem of
the limits imposed by the control units. Then they went on
to map the benefits they could achieve by plotting different
multiple injection sequences (two secondary injections very
close to the main injection; one secondary injection not too
close to the main injection plus two closely-spaced
secondary injections; one secondary injection and then two
main injections close together after a certain period, etc.)
against different engine service conditions: in the idling
region; with low loads and low rpm; with high rpm and
moderate load; with low rpm and high load, etc..
The study revealed the potential of the system and showed
that great benefits are achievable in all cases, though
these tend to focus on one field or another according to the
type of sequence chosen and the engine service area
targeted. In some cases, for example, the priority is to
reduce start-up times and fume levels, in other cases it is
to increase torque and reduce noise while in others still it
is to reduce emissions and ensure a quieter drive. And now
this research strand has led to the creation of the Multijet
engines, including the brand new 90 bhp 1.3 JTD Multijet 16v
which debuts on the Grande Punto.
|
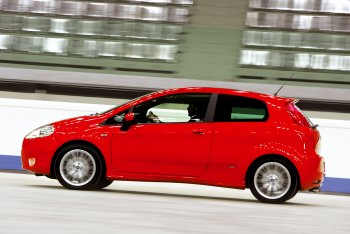 |
|
|
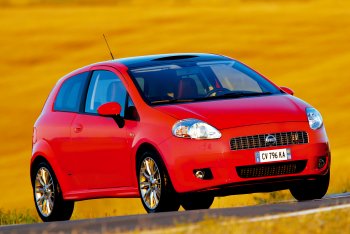 |
|
The novelties in the Fire family
The 65 bhp 1.2 Fire 8v
The tried and tested 1242 cc Fire engine makes its debut on
the Fiat Punto with a number of refinements designed to make
it a champion of thriftiness where consumption is concerned,
but without detracting from performance. The engine delivers
48 kW (65 bhp) at 5500 rpm and takes the car to a top speed
of 155 km/h.
That is not all. With the 1.2 8v engine, the new car has
very low fuel consumption, among the best in its category.
The merit goes to the engine configuration, which aims to
achieve generous torque at very low revs (with benefits in
terms of enjoyment and elasticity), and to the ratios chosen
to optimise the balance between performance and consumption.
The result is torque of 10.4 kgm (102 Nm) at 3000 rpm and
consumption of 7.9 l/100 km (urban cycle), 5.1 l/100 km (out
of town) and 6.1 l/100 (combined cycle). Interesting results
which were achieved with a few effective improvements. For
example, new inlet and exhaust manifolds, a new combustion
chamber (with the compression ratio now 11:1), and new cam
profiles to optimise the fluid dynamics of the engine, thus
improving efficiency.
Also with the target of reducing consumption, the engineers
chose an active knock sensor, capable of managing the
advance efficiently in all conditions and, above all, the
Marelli phased sequential multipoint injection system, which
was only available on more sophisticated engines until a
short time ago. The new model adopts a 'drive by wire'
system which eliminates the mechanical link between the
accelerator pedal and the throttle valve, significantly
improving the torque delivery on the basis of the driver's
demands, translating it into benefits for the customer in
terms of driveability and consumption.
Where performance is concerned, we should underline the use
of an electronic control system developed for the car and
based on a new generation Marelli electronic control unit,
capable of dialoguing in a network with the electronic
devices on the car through serial lines. The quality of life
on board also improves as a result of the optimised
performance of the inlet and exhaust systems, the
optimisation of the coupling tolerance between the
crankshaft and the crankcase, the computerised selection of
the main bearings, and the development of a specific method
to install the engine in the engine bay. This also reduced
the amount of vibration transferred from the engine to the
bodyshell. A special barycentre system was adopted to
support the engine, with two blocks plus a reaction link
that acts as a tie rod, with the result that the new
supports are aligned on an axis that passes through the
engine's centre of gravity, to obtain reaction forces with a
neutral link.
An efficient engine, and a clean engine. Where the
environment is concerned, the 1.2 8v respects EC phase 4
anti-pollution standards, thanks to the new AISI steel
exhaust manifold with a catalytic converter in the engine
bay, welded on the flange of the exhaust manifold. The
device is very efficient in this position, because it can
reach high temperatures more rapidly, reducing emissions
while the engine is still heating up. The equipment present
on the Grande Punto 1.2 8v to reduce its environmental
impact includes a returnless fuel supply system, which
eliminates the recirculation of fuel inside the tank and
reduces the formation of fumes.
And finally, to improve reliability the coils have been
mounted close together in a single block. This new type of
coil reduces shock absorber wear, making more energy
available to ignite individual spark plugs because the lost
spark has been eliminated, easier cold starts because more
energy is available for the spark plug (more energy supplied
by the coil and no losses during the high voltage transfers
because very short cables are used) and, finally, a
significantly reduced risk of interference to the onboard
equipment from high voltage cables.
The 77 bhp 1.4 Fire 8v
The new engine has a capacity of 1368 cc and four cylinders
in line, with a bore of 72 mm and a stroke of 84 mm. There
are two valves per cylinder, activated directly by the
overhead camshaft. The engine was developed paying
particular attention to performance and consumption, areas
in which the Fiat Punto leads its category. This is achieved
as a result of the volumetric efficiency, which has been
optimised throughout the operating range, thanks to careful
fluid dynamic development of the entire inlet system and the
timing. The result is a power output of 57 kW (77 bhp) at
6000 rpm and a peak torque of 11.7 kgm (115 Nm) at 3000 rpm.
With this engine, the Fiat Punto has a top speed of 165
km/h, and accelerates from 0 to 100 km/h in 13.2 seconds.
Consumption figures are among the best in this segment: 7.7
l/100 km in the urban cycle, 5.2 l/100 km out of town, and
6.1 l/100 km in the mixed cycle.
An engine that is both brilliant and sparing on fuel. This
performance is helped by the adoption of an electronic
throttle valve control system known as 'drive by wire', and
in particular by the use of a new high turbulence combustion
chamber which is combined with continuous variable valve
timing, governed by the control unit. This innovative system
allows a significant part (about 25%) of the exhaust gases
to be recirculated in the combustion chamber, significantly
reducing fuel consumption and exhaust emissions when driving
with a partial load. Last but not least, like the 1.2 8v,
this engine also features a number of changes designed to
reduce consumption. For example, the timing components are
lighter and the valve springs are of the low load type to
reduce friction.
Another feature of the new 77 bhp 1.4 is the higher
compression ratio (11:1) and the high torque delivery at low
speeds, features that have made it possible to lower fuel
consumption. This target was also achieved by the
calibration of the latest generation engine control system,
which managed to reduce consumption further, compatibly with
the demand for handling, performance and low emissions. In
the latter field, we should underline that the 77 bhp 1.4
Fire engine also respects Euro 4 standards, thanks to a
catalytic converter positioned in the engine bay (welded
onto the exhaust manifold flange using a new technology),
and it reaches a high temperature very rapidly, cutting
emissions even while the engine is heating up. The equipment
on the new car to reduce its environmental impact includes a
returnless fuel supply system, which eliminates the
recirculation of fuel inside the tank and reduces the
formation of fumes.
High performance, low consumption and cleanliness: the 77
bhp 1.4 combines these winning features with excellent
acoustic comfort. In addition to the technical improvements
described for the 1.2 Fire engine, this engine also features
a flexible flywheel that reduces the vibration transmitted
from the engine to the bodyshell.
Reliable, sophisticated gearboxes
A range of reliable, strong, sophisticated gearboxes was
developed to match the engines available on the Grande Punto,
and these components are an important aspect of enjoyment
and comfort (robotised Dualogic gearboxes will also be
available after the launch).
A new dual hose control was developed for all the gearboxes,
to insulate vibration, guaranteeing more precise manoeuvring
and quieter operation. It is a new generation,
technologically advanced device, which uses high performance
technopolymers extensively, on the basis of the different
resistance, weight and self-lubricating characteristics.
Plus the fact that bench testing in extreme climate
conditions has helped to refine materials, couplings and
processes, guaranteeing the utmost sturdiness and
reliability of the product. What is more, the quality and
reliability of these components is guaranteed by the
painstaking care that goes into their assembly, during which
all the components are pre-tested and all the 'values' that
define efficiency, elasticity and tolerances are measured
electronically.
All versions adopt the hydraulic clutch disengagement
control, with an external actuator on the 1.2 and 1.4 Fire
and 1.3 Multijet engines, and a coaxial clutch release
mechanism (CSC) on the 1.9 Multijet. The device, which has
no external actuation components, increases the efficiency
of the system throughout the life of the car and also
insulates the noise and vibration coming from the engine.
Compared to a hose control, the hydraulic control guarantees
automatic adjustment of pedal wear; on the JTD versions,
this system is combined with a device that takes up the
clutch plate wear so that the load of the clutch pedal
remains constant for the car's entire life. To comply with
European legislation to protect the environment, all
versions, both petrol and diesel, adopt friction materials
that only contain environment-friendly elements. And the
clutch pump has a plastic body, which helps to lower the
weight, a steel cylinder and a plastic piston.
The 5-speed gearbox for the 1.2 8v and 1.4 8v engines
Enhanced acoustic comfort, reduced engagement effort even
when cold, and more precise gear engagement. These are the
advantages of the C514 gearbox (a transverse configuration
with two shafts in a cascade and one differential), which
was optimised by changes to: the gears, synchronisers,
lubrication, internal gear control and clutch control.
Combined with the 5-speed Fire 1.2 8v and 1.4 8v engines,
this version represents the maximum upgrade of the gearbox
in terms of transmissible torque (15 kgm). The use of nobler
materials for the gears, the adoption of a more powerful
differential with larger conical gears and the screw
connection between the housing and the crown all improve
reliability. The main features are excellent manoeuvring of
the gear lever, quiet operation and low weight.
What is more, the gearbox adopts a gear control which,
thanks to stroke limiter selection, protects against the
risk of involuntarily engaging reverse, and makes engagement
of fifth and sixth speeds more precise. And finally, the use
of gearing made of quality materials and of a completely
redesigned differential, made it possible to strengthen the
gearbox itself, which in this configuration can transmit up
to 15 kgm of torque.
The most significant technical features are the gearing and
clutch housings, which were optimised to lower the weight
and to absorb noise better, using FEM (Finite Element
Method) calculation techniques. Plus Borg-Warner free-ring
synchronisation on all gears. And finally, a dual cone
synchroniser on first and second, the gears used most
frequently, with an engagement effort that is 40% lower than
the effort required with a conventional single cone
synchroniser.
The internal gear control system has four selection levels,
with a central positioner and bearings. Lubrication is
dynamic, and the oil flow is channelled through bore holes
in the housing. The advantages are less wear and more
efficient torque transmission, and manoeuvrability even at
low temperatures.
The 5-speed gearbox for the 75 bhp 1.3 Multijet engine
The C510 is extremely easy to manoeuvre and very quiet. It
has a transverse configuration with two shafts in a cascade
and one differential. In this case too, the gearbox has been
optimised, adopting a dual cone synchroniser on first and
second, and a highly efficient reverse engagement control.
Two improvements that guarantee the product's excellence
where manoeuvring is concerned. Lubrication is dynamic and
the oil is channelled through bore holes in the housing and
on the shafts. The maximum torque transmissible is 21 kgm.
The 6-speed gearbox for the 120 bhp and 130 bhp 1.9
Multijet engine and the 90 bhp 1.3 Multijet
The M20 and M32 gearboxes belong to a new family of
three-axis transmissions, designed to give better
manoeuvring and to be more compact than traditional two-axis
gearboxes. Available with 6 speeds, these two units can
support high torque (230 Nm and 320 Nm), so they are the
ideal for high performance diesel engines: the 90 bhp 1.3
Multijet (M20) and the 120 bhp and 130 bhp 1.9 Multijet
(M32).
In this case too, the engineers' goal was to improve
acoustic comfort, to eliminate any vibration or shaking of
the gearshift, and to reduce actuation and engagement effort
even when the engine is cold. The gearbox (with three shafts
and a built-in differential) has small axial measurements,
and is easy to manoeuvre in all speeds, and extremely quiet.
The credit goes to a number of innovative solutions that
were already employed on earlier gearboxes, such as free
ring synchronisers, dual-cone synchronisers on first and
second, and dynamic lubrication. |
|